How to pick valve springs for your race car
It could be said that valve springs are the unsung heroes of horsepower. Tasked with a critical job of controlling the valve train, valve springs operate in a harsh environment. They are rapidly cycled while being subject to great force, friction, and heat. It goes without saying that high-performance valve springs are a must in any racing application, and selecting the right coils can be the difference between making reliable horsepower and not making it to the finish line.
“Valve spring are just one component of the valvetrain system,” said Chris Osborn, product engineering manager at PAC Racing Springs. “The springs provide force to keep the valve in contact with the mating components during the valve opening, peak lift, and during closing events of the intake and exhaust cycles. The spring has to maintain that force at a rate of nearly 100 times a second, without losing any load or failing run after run. Many times, the engine speeds are limited by the ability of the springs to maintain this force, so they become an extremely critical component of any engine.”
There are a few factors that make it necessary for drag racers to run high-quality valve springs. Increased rpm, high-lift camshafts, and increased durability are just a few reasons. There are also many variations of valve springs, so it’s important to select the best coils for your application.
Pro Stock cars use camshafts with lift in excess of 1-inch. This puts a whooping on valve springs so they are checked after every pass.
Common spring shapes are cylindrical, beehive, and conical. In addition, you’ll find dual and triple springs in some applications, and there are a few common spring materials, and different size and shape wire, too.
“Valve springs are extremely high-stressed components, if not the highest stressed in the entire engine,” added Osborn. “They need to have specific alloys and manufacturing methods to be able to withstand the lift and rpm to which they are subject. Almost all high-performance valve springs are produced from chrome-silicon steel alloys specified in material standard ASTM A877. The valve-spring wire goes through extensive levels of inspection and control to maintain cleanliness within the steel and maintain high ductility with high-tensile strength. These alloys have varying amounts of silicon, vanadium, nickel, molybdenum, and carbon that provide various levels of performance with tensile strengths over 300 ksi. PAC Racing Springs has developed its own alloy that has been around for years and is known as ‘PACaloy.’ This is a specific spring material for the racing industry that optimizes the alloys with the mechanical properties to provide exceptional fatigue life with minimal load loss.”
He continued, “The lightweight nature of titanium is great for valvetrain parts, but the rapid development of the chrome-silicon steel alloys in the past decade have created a large decline in its use. Titanium is expensive with a limited lifetime, and the dual-spring designs that PAC Racing pioneered over the last decade have rivaled the weight advantage of titanium with superior life with a much more advantageous cost/run factor.”
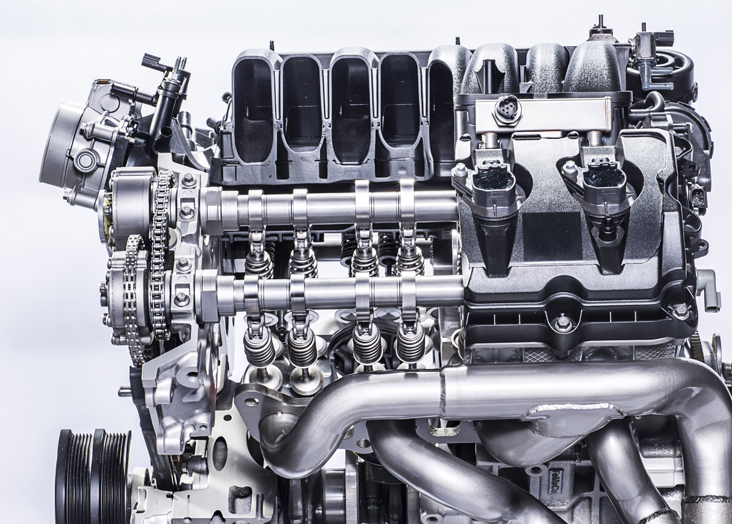
Spring Selection
Picking the right springs can be a daunting task. Spring selection is often determined by camshaft configuration, class rules, budget, and the physical room in the cylinder head (when machining is not allowed). “The first step is usually to discuss required forces with the cam designer,” said Jeff Villemure, engineer at Performance Springs, Inc. “They will take into consideration the acceleration of the cam lobe, max engine rpm, and the weight of the valvetrain. A few calculations go into determining the forces needed to control the valvetrain, but a lot has to do with history and experience. Also, consider the cylinder-head package size (and the retainer) to determine a spring that fits best.”
Osborn added, “Spring selection is not a simple process. You have to start with knowing what size spring can you fit in the cylinder head, the installed height, and valve lift. Determining the load and rate are more challenging questions to answer. Newton’s second law of motion, F=MA, comes into play since F is the spring force, M is the mass of the components (valves, retainer, rockers, pushrods, etc.), and A is the cam/valve acceleration at a given engine speed. The best starting point to determine spring loads is from cam suppliers, spring suppliers, or engine builders who have experience with all of the components that go into a particular engine. Companies like PAC Racing Springs have sophisticated software, Spintron test equipment, and the experience to help determine the optimum spring selection.”
Jack McInnis, of Erson Cams, stated, “There are a number of factors involved in selecting the optimal valve-spring setup for your engine. The type of camshaft and lifters (hydraulic or mechanical), the aggressiveness of the cam profile, weight of the valves, and valvetrain components, rocker arm ratio, and rpm range will be determining factors. Sometimes, other considerations are present as well, such as the type of cylinder heads. Modular fords, for example, have limited clearance for up-rated springs. Having all this information at hand will help greatly when you contact the manufacturer for a recommendation. Ultimately, you are looking for the spring which best controls the valve movement in your specific application with the related components you will be using.”
Many racers have made the switch to beehive springs. “Beehive springs have been around for a very long time (Wright Brothers Engine, 1903), and many OEM companies use them in current engines,” said Osborn. “Anytime the mass of the valve side of the valvetrain is lighter then the engine will have better valve control and rpm capability. The beehive spring does this by allowing the retainer to be smaller with less mass. The spring also has reduced mass on the moving end. The beehive spring essentially combines two springs into one. The conical top with the straight spring provides two different spring rates, and that can also improve the ability to control the valve at high speed. Most beehive springs that PAC Racing Springs produces utilize multiarc or ovate wire that allows the use of more coils at the bottom of the spring to further enhance the damping and control with the spring.
“Beehive springs provide many great benefits described above. However, they are still just a single spring and can only provide so much force before the stresses become too great and a dual spring is required. Beehive springs are great for most engines that have cams with 0.600-0.650-inch lift with relatively lightweight valves and moderate cam profiles. PAC Racing Springs has beehive springs that can handle higher lifts, but ‘smooth’ cam lifts are required to avoid excess stress.”
McInnis added, “The conical shape of a beehive spring reduces the overall size and, more importantly, the weight of the retainer. Reducing the weight of the valvetrain components means the valve springs can do their job with lower spring pressure, which in turn reduces stress on the entire valvetrain. The reduced diameter at the top of a beehive spring also provides greater spring-to-rocker arm clearance. Racers could consider using beehive springs for many hydraulic lifter applications. The lighter retainer weight is more important with hydraulic lifters because the spring pressure must be limited for the lifters to function and survive. With solid/mechanical lifters, you can increase spring pressures significantly to control the valve movement. With solid lifters, it is advisable to always err on the side of higher rather than lower spring pressures.”
Don’t Float
Valve float is a major problem and can be a real engine killer. “The term ‘valve float’ is misleading, though, as it generally is assumed to be when the valve motion at peak lift exceeds what the cam/rocker can provide,” said Osborn. “This is what is more commonly referred to as valve loft. Actually, lofting the valve can help make power if it’s in the right spot. Too much loft in the wrong areas can bend valves when they contact pistons. What is more detrimental is when the valve closes at such a high rate of speed that the valve will bounce off the seat. This is referred to as valve bounce (see Valve Motion Chart). High levels of valve bounce will damage the valvetrain catastrophically with broken valves, rockers, cams, and springs. Valve bounce is what you hear when the engine is running too much rpm and it sounds like everything is falling apart. This is especially noticeable on a Spintron test stand. All of this is corrected with matching valvetrain component selection, especially the valve springs.”
He continued, “Valve bounce degrades engine performance with dips in the power curve, which may be observed in a dyno test session. Then, you have to ask, is the valve lash changing? Excessive valve bounce creates high loads in the system and can cause lash changes due to valve stretch or valve seat beat-in. If you try to take a spring off and the retainer and lock are very difficult to disassemble, this may be occurring. And, in the worst cases of valve bounce, the tips of the springs can break off. Sometimes, valvetrain control can be improved by shimming the spring up to run closer to coil bind as long as it does not go past the bind height recommendations.”
McInnis added, “Indicators of valve float are when an engine goes flat or stops accelerating at the upper rpm range. Sometimes, it seems to pick up a high rpm misfire. Also, carbon residue from reversion in the intake manifold, this would generally indicate prolonged problems, like you notice it after blowing up the engine. Other indicators of float might be when adjusting lash, noting that a rocker roller is moving around the outside edges of the valve. Also, you may find lash tightening up due to valve stretch from impacting the seat. Some titanium valves can erode by the seat materials, notably ductile or powdered-metal seats.”
Bind is Bad
Along with avoiding valve float, it’s important to prevent coil bind. “Springs should be compressed in a checking station or very cautiously in a bench vise to determine the exact height where all the coils touch and they become solid,” said Osborn. “It is OK to take a high-end spring and compress them solid. All PAC Racing valve springs are taken solid several times during the manufacturing and inspection process.
"This needs to be done with a retainer that compresses the inner spring as well as it may go solid before an outer spring. This coil-bind height number is recorded. This is compared to the installed height and valve lift that is measured on an engine. The difference is the coil-bind clearance number. This number needs to positively show there is clearance. This clearance can be modified with shims, retainers, locks, or spring selection to tune the valvetrain for optimum performance.”
McInnis said, “When installing valve springs, check every spring individually for correct installed height, tolerances can vary as much as 0.050-0.060, which can be enough to cause coil bind in an individual spring while others are fine.”
Performance Springs Inc. has an easy-to-use online calculator (psisprings.com) to verify the intended valve lifts and installed heights will not cause coil bind with each part number. “Some engine builders account for valvetrain deflection in their calculations, but they should be aware that valvetrain deflection may be released at high speeds. PSI inspects each spring for load and coil bind. The advertised coil bind is the maximum that will be shipped.”
Checking Your Springs
“Checking springs consists of pulling the valve cover, looking at the springs and everything in the valvetrain area to see if anything stands out like loose or broken parts, springs, spring tips, etc.,” explained Osborn. “Ideally, the spring loads are measured with an on-head valve-spring load tester. These loads should be recorded after the engine has been broken in and then checked periodically. These loads may not correlate exactly to a bench tester, but it does give a measure that can be compared run after run. Your level of racing dictates how often springs are checked. Pro Stock engines that run 10,000-plus rpm with 1.200-inches of lift get checked after every pass, whereas a bracket race engine with 7,500 rpm limit and 0.800-inch lift cam may only need to be checked once a year. A proper maintenance schedule based on the level of racing is what is required. Again, cam companies, spring companies, or engine builders can help determine the checking frequency based on your level of racing.”
Villemure added, “How often you check springs depends on how long the springs are expected to last. Pro Stock racers will check them every round, but they don’t expect springs to last longer than four to eight passes. Springs used in some Sportsman engines can last hundreds of passes, so racers typically inspect them after a full weekend or more. If a racer is checking lash or has the valve covers off for any reason, it would be wise to look over the springs and check them with an ‘on-head’ tester.”
Lastly, every racer should have a tool for checking valve-spring tension. “An on-head tester is great for quick load measurements, to make sure the springs are maintaining their installed loads,” said Villemure. “A cylinder head installed height measurement tool is also important for initial setup.” McInnis recommends some type of spring pressure gauge, these are a baseline tool and will never read exact spring pressure due to pivot length of rocker, pushrod, etc. Also, have a way to change springs on the assembled engine as well as feeler gages, a flashlight to check for broken inner springs, and tools for adjusting lash.
Osborn agrees that an on-head spring-load tester should be used to determine if there is any load loss occurring. He also mentioned that feeler gages can be used to see if lash is changing. This will ensure the valvetrain (including springs) is working well. And use a flashlight to look all around the springs and a magnet to see if there are any spring tips or metal in the top end of the engine. Also, he recommends using a log book to record how many runs are on the springs and spring loads.
Valve Spring Dos & Don’ts
Do: be careful when handling springs. They are one of the highest stressed components in an engine and should be handled with care.
Don’t: put a spring in a vise to hold them on the OD of the spring. Compressing the sides will cause failure.
Do: check to make sure the springs fit in the cylinder-head pocket. Interference can cause failures.
Don’t: let the springs get rusty. The rust pits will create failure initiation points.
Do: check to make sure the spring retainers fit the springs. Too much interference can break end coils.
Don’t: modify the springs by grinding the ends. Contact your spring supplier if you feel this is required.
Do: check to make sure the valve-spring retainer clears the rocker arm and valve-stem seal for the full lift.
Do: store valve springs in a low humidity environment away from water or chemical spills. Do not run any springs that show signs of corrosion. This is one of the most common reasons for premature fractures in springs.
Don’t: install springs with excessive clearance. Err on the side of more pressure except with hydraulic or flat tappets. Make sure that adequate oil is present for cooling the springs. In the event of an excessive temperature/overheating event, you should always check the springs before your next outing. Overheating can affect the spring pressure permanently.
SOURCES
Erson Cams / 800.641.7920 / PBM-Erson.com
PAC Racing Springs / 877.799.9417 / RacingSprings.com
Performance Springs, Inc. / 248.486.3372 / PSISprings.com